The K-positioners can manipulate products ranging from several to even 3000 kg. Each of the positioners can be immediately delivered with standard configuration or can be prepared in a special design that accommodates the individual needs of the application. K-positioners are based on the concept of modular construction. This makes it easy to modify the positioner and adapt it to the changing production needs.
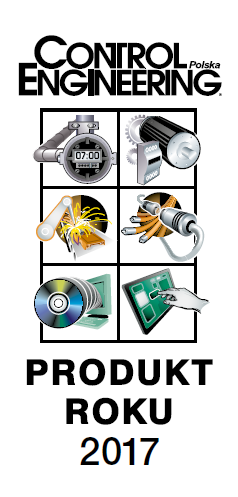
- Modularity
- Easy reconfiguration
- Powerful and reliable components
- Native integration with Kawasaki robots
- Short delivery time
- Complete range of positioners
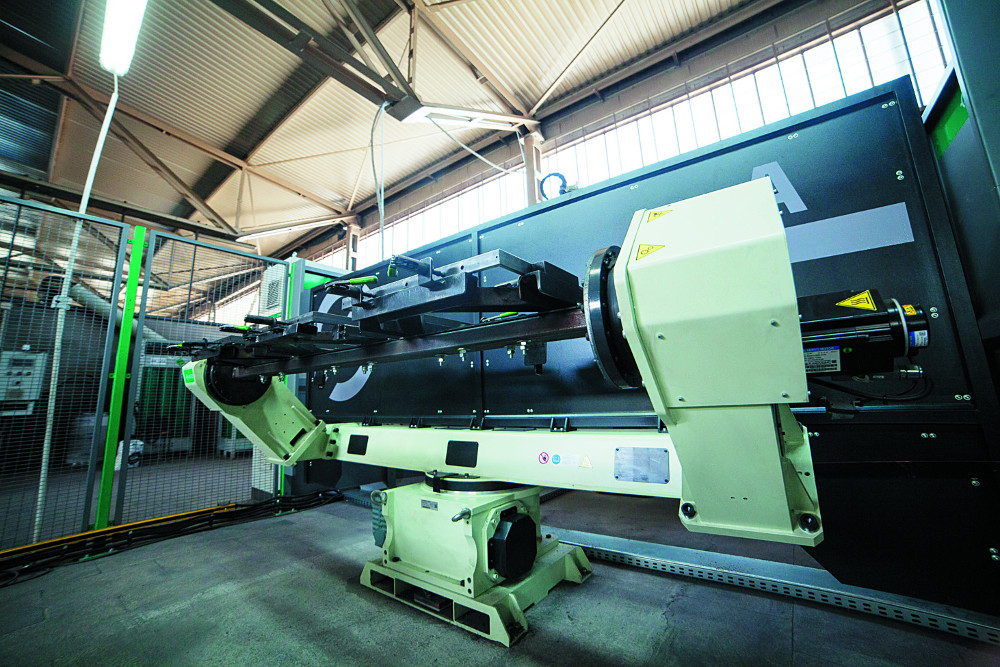
|
|
|
---|---|---|
Time-consuming |
Short delivery time - READY POSITIONERS FROM THE STOCK |
|
High risk |
SHORT INTEGRATION TIME |
|
Expensive (prototyping, mechanical modifications) |
Low risk –all main components are same with Kawasaki robot components, |
|
Economical risk (big part of work has to be done before getting final order) |
No expenses before getting final order from the customer |
|
Built-in welding ground transfer system |
||
EASY RECONFIGURATION OF THE SYSTEM |
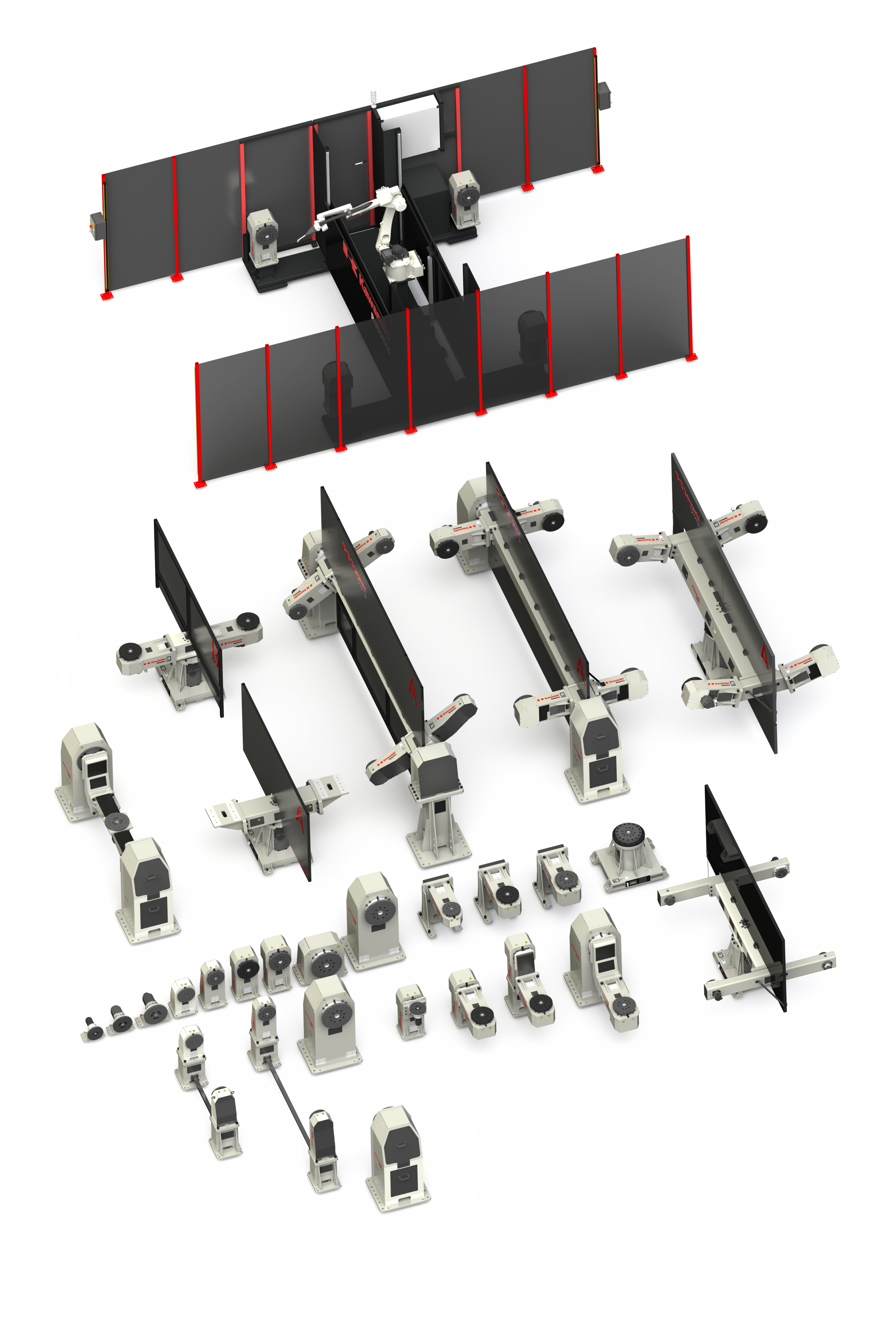
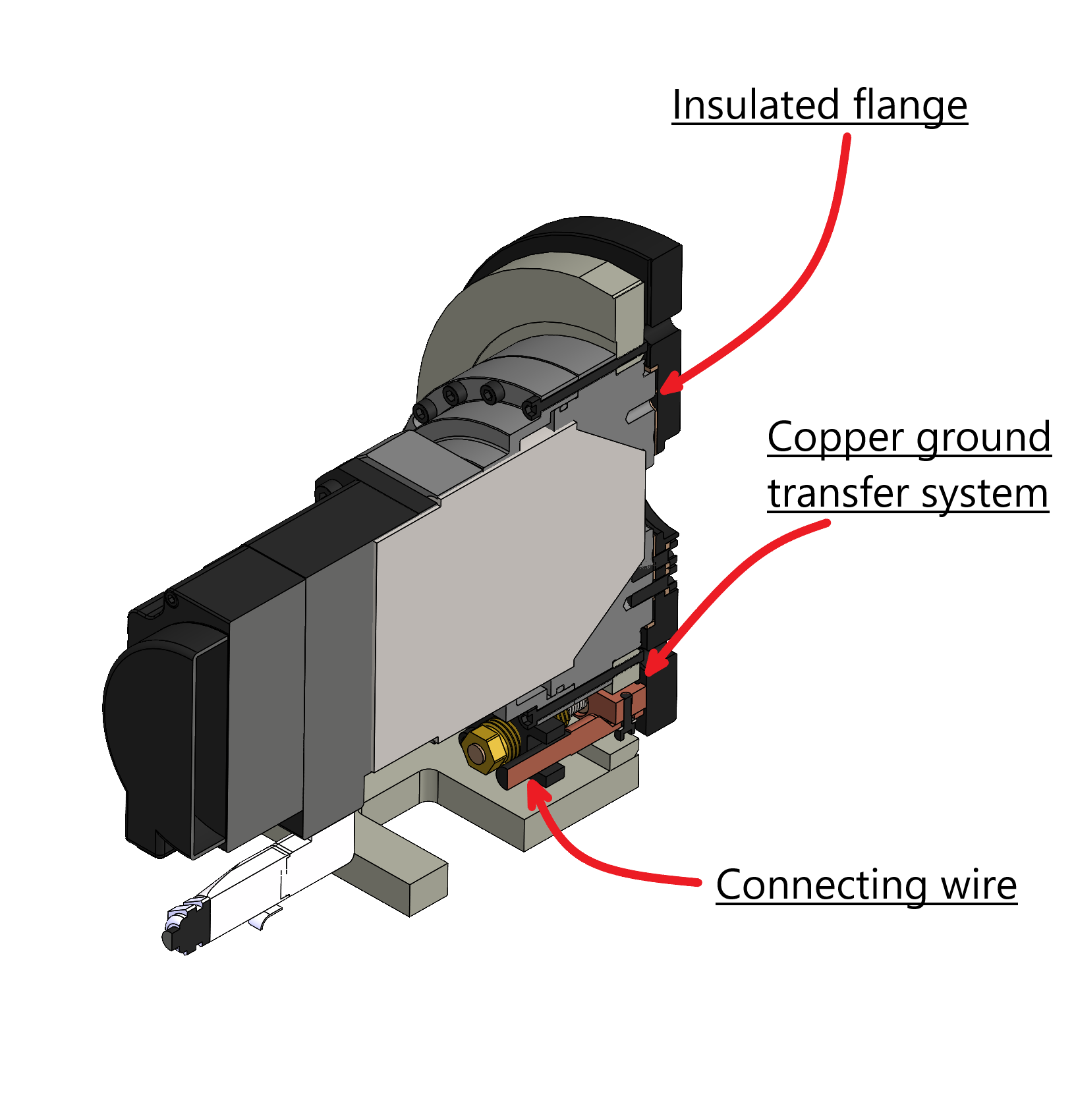
- General purpose single axis positioner - basic modul
- Horizontal rotating axis
- Kawasaki external axis (E0x controller)
- Welding ground transfer system
- Payload 125, 250, 500, 1000, 2000kg
- Eco version for payload 250, 500 and 1000kg
PST125
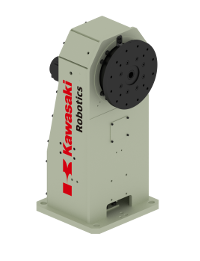
PST250
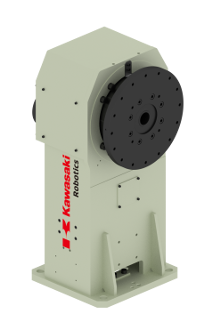
PST500
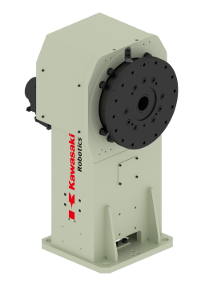
PST1000
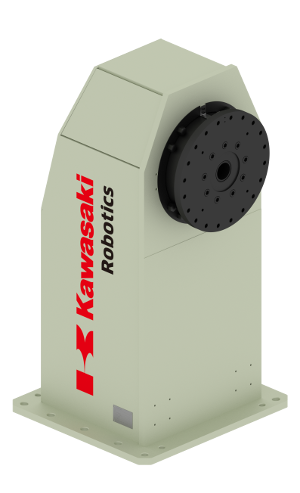
- General purpose single axis positioner
- Horizontal rotating axis
- Supporting unit - extended length of workpiece
- Pedestal unit- extended workpiece dimension
- Welding ground transfer system
- Kawasaki external axis (E0x controller)
- Payload 250, 500, 1000, 1500, 3000kg
- Eco version for payload 250, 500 and 1000kg
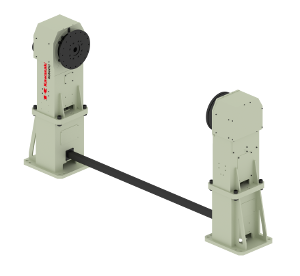
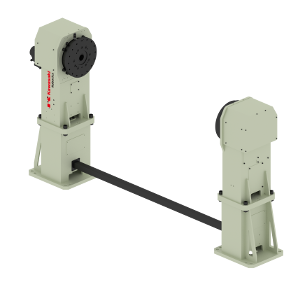
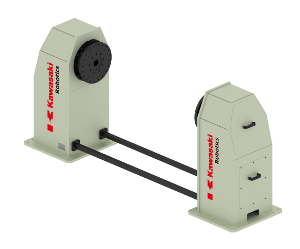
- General purpose double axis positioner
- Horizontal rotating axis + Vertical rotating axis
- Welding ground transfer system
- Kawasaki external axis (E0x controller)
- Payload 125, 250, 500kg
- Eco version for payload 125, 250, 500kg
PST125-F2
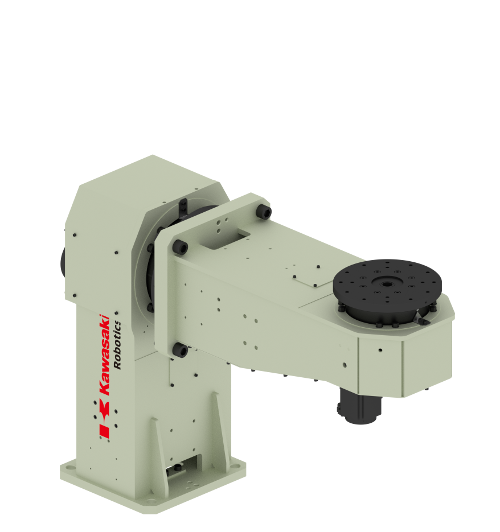
PST250-F2
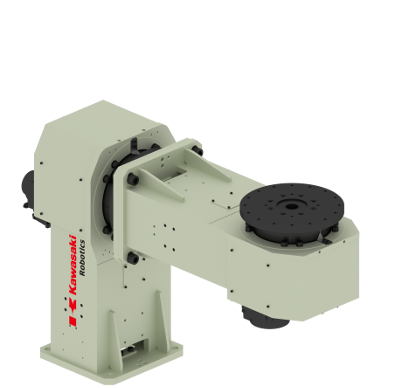
- General purpose double axis positioner
- Horizontal rotating axis + Vertical rotating axis
- Pedestal unit - extended workpiece dimension
- Welding ground transfer system
- Kawasaki external axis (E0x controller)
- Payload 125, 250, 500kg
- Eco version with payload 125, 250, 500kg
- Long version with payload 250kg
- High version with payload 500kg
PST125-L2
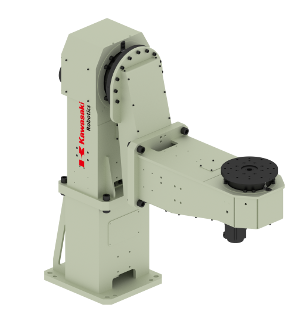
PST250-L2
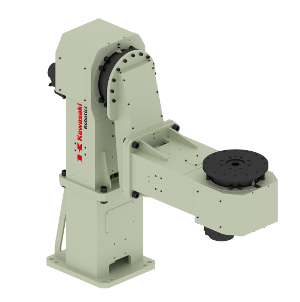
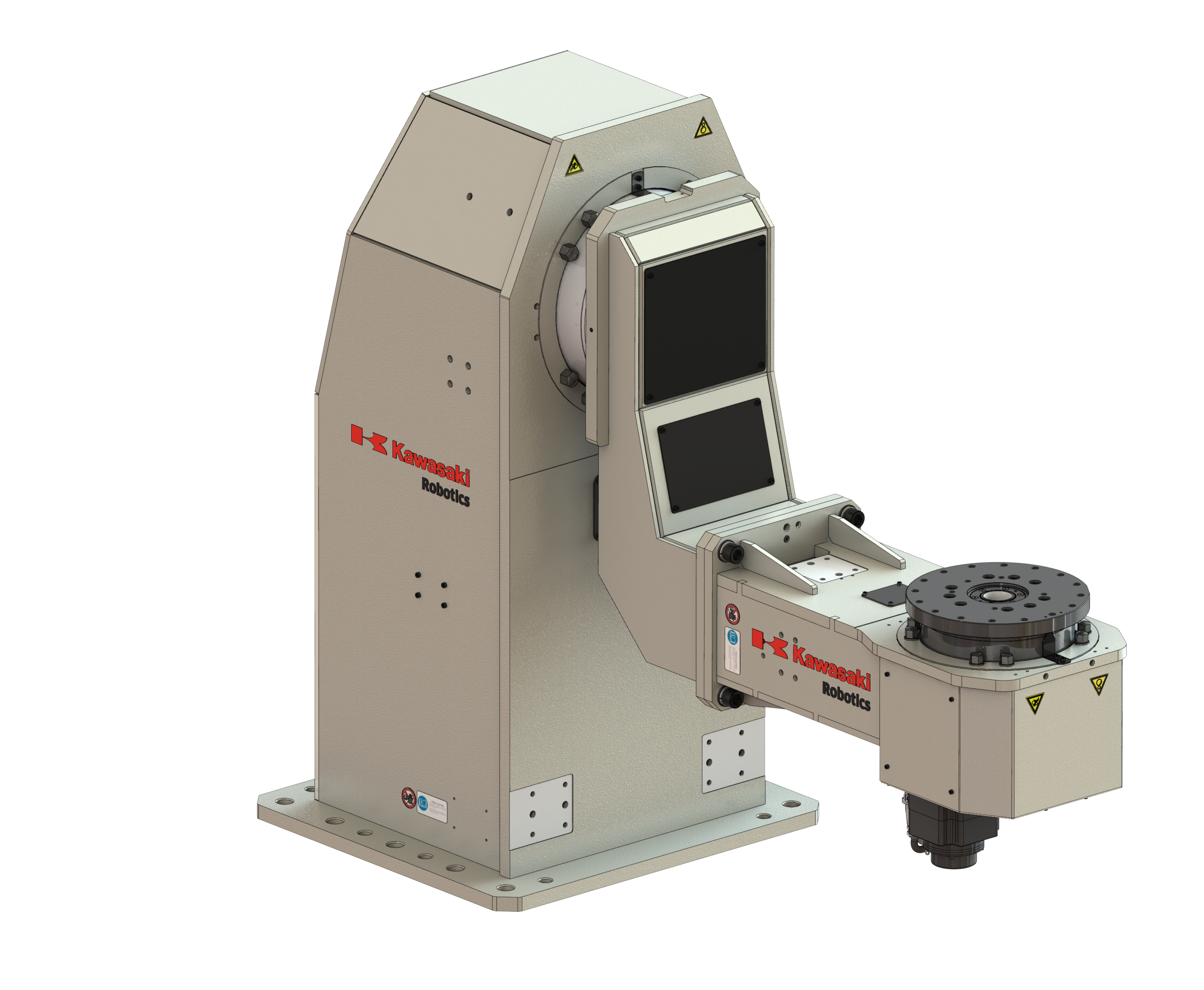
- General purpose multipositioner
- Vertical rotating axes + 2 Horizontal rotating axis
- 2 stations
- Welding ground transfer system
- Kawasaki external axis (E0x controller)
- Payload 125, 250, 500, 1000 kg per side
- Distance between flanches 2500-4000
- Flex and Compact version
PST125-M3H2V1-x
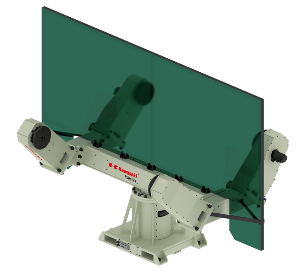
PST500-M3H2V1-x
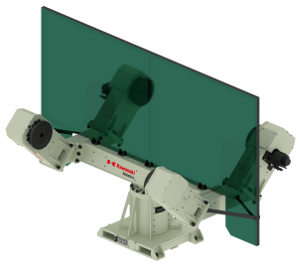
- General purpose multipositioner
- 3 Horizontal rotating axis
- 2 stations
- Welding ground transfer system
- Kawasaki external axis (E0x controller)
- Payload 125, 250, 500, 1000 kg per side
- Distance between flanches 2500-4000
PST250-M3H3
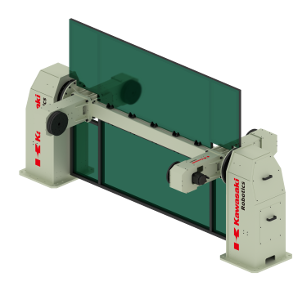
PST500-M3H3-x
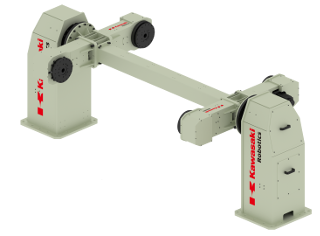
- General purpose linear track for small and big robots - basic modul
- Kawasaki external axis (E0x controller)
- Maximum payload 3000 kg
- Length up to 30m
- Optional pedestals, support pillars, rotational and linear axes, carbon cover and slave carts
TRK500

TRK1000
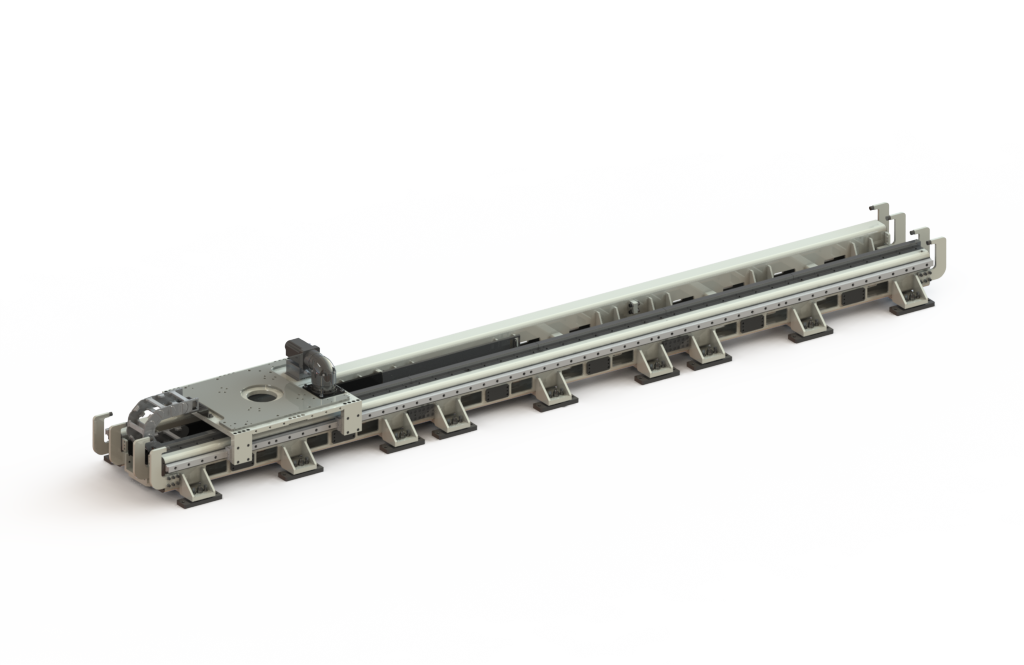
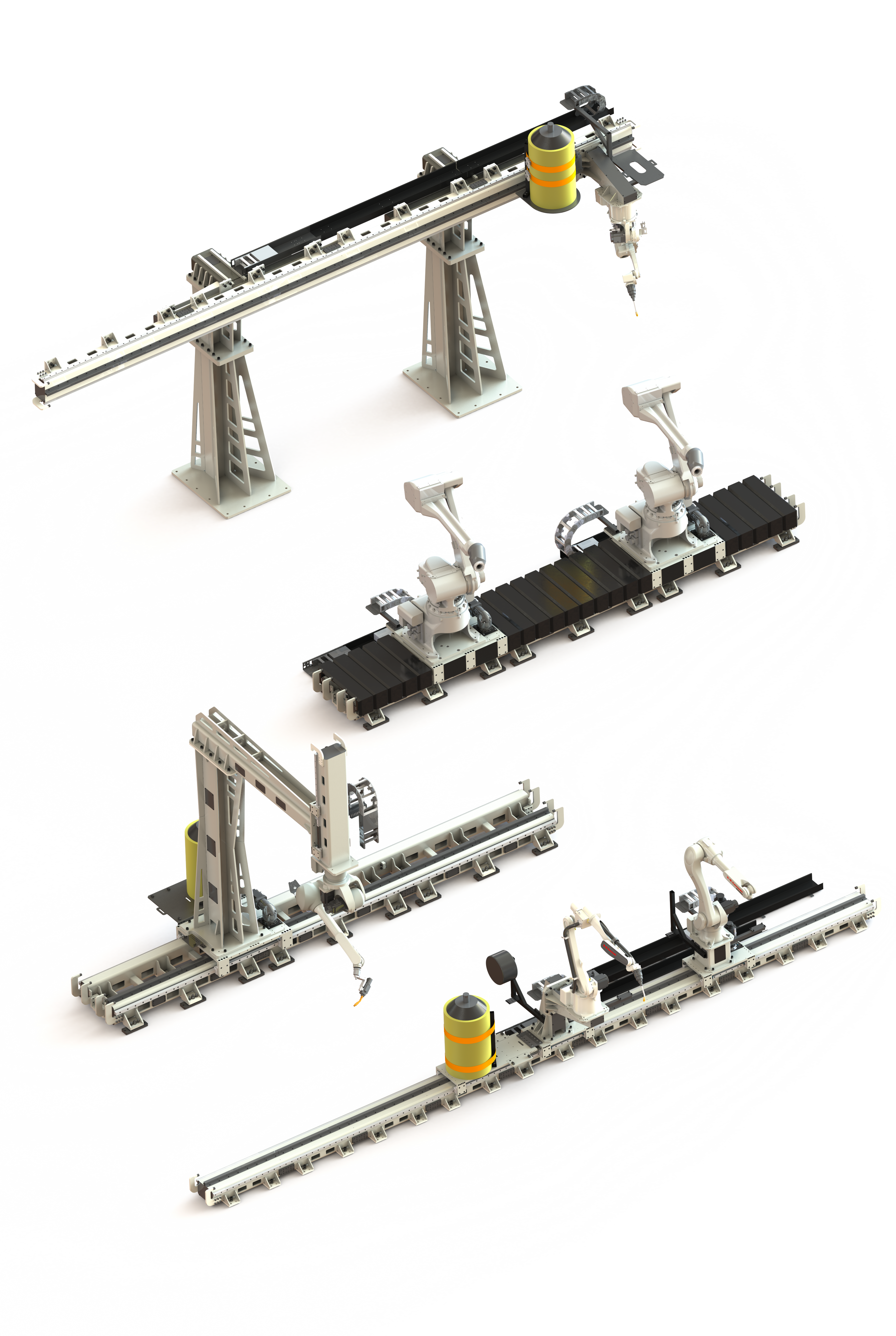
Welding station
with two positioners
Components
- Kawasaki industrial robot series BA or RA
- Fronius welding power source
- Tooling (a wire feeder, welding torch,
anti-collision connector) - Welding Fume Extraction and cleaning station
- Two positioners with support up to 2000kg payload
- Safety system to protect robot's work zone
Workpiece
- Simple and quick installation
- Double productivity
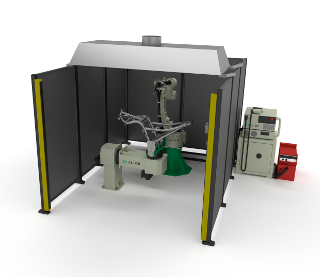
Welding station
with double axis positioner
Components
- Kawasaki industrial robot series BA or RA
- Fronius welding power source
- Tooling (a wire feeder, welding torch,
anti-collision connector) - Double axis positioner with 250kg payload
Workpiece
- Complex geometry
- Always optimal welding position
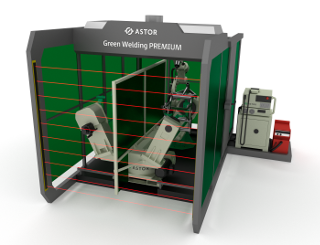
Welding cell
with multipositioner
Components
- Kawasaki industrial robot series BA or RA
- Fronius welding power source
- Tooling (a wire feeder, welding torch,
anti-collision connector) - Positioner H (2 stations) with 250kg payload per side
- Common frame for guaranteed positioning
- Safety system to protect robot's work zone
- Welding Fume Extraction and cleaning station
Workpiece
- Complex geometry
- Long workpieces
- Always optimal welding position
- Double productivity
Wiśniowski
„We are automating those processes where robotization delivers tangible benefits. Through the use of state of the art technologies, we’ve improved the quality of our production processes, and, perhaps even more significantly, the safety of our operators. Currently we are delivering excellent weld quality and high productivity” - Maciej Socha, Fencing Systems and Corrosion Protection Director
Targets
- Increase productivity
- Increase production process quality
- Improve operator safety
Benefits
- Reduced lead times
- three-fold efficiency increase in the robotized gate welding process
- Excellent weld quality achieved through robotized welding
Wasiak Gruppe / POLMO SA
“Robotization ensures high quality of products and optimizes product cost. It makes winning contracts easier for us” - Marek Wasiak
The welding cell with Kawasaki BA006L robot and E01 controller, based on the H-frame with double cells. There is a possibility to load the elements for processing at the first station, while at the same time the details are being welded by the robot on the second side. The modular construction enables simple and quick installation at the client’s premise.
Operating benefits
- optimization of the welding process and its service
- precise determination of the cell availability
- increase of the workers’ safety
Economic benefits
- increased margin on the individual produc
- prevention of HR deficiencies
- fast return on investment